
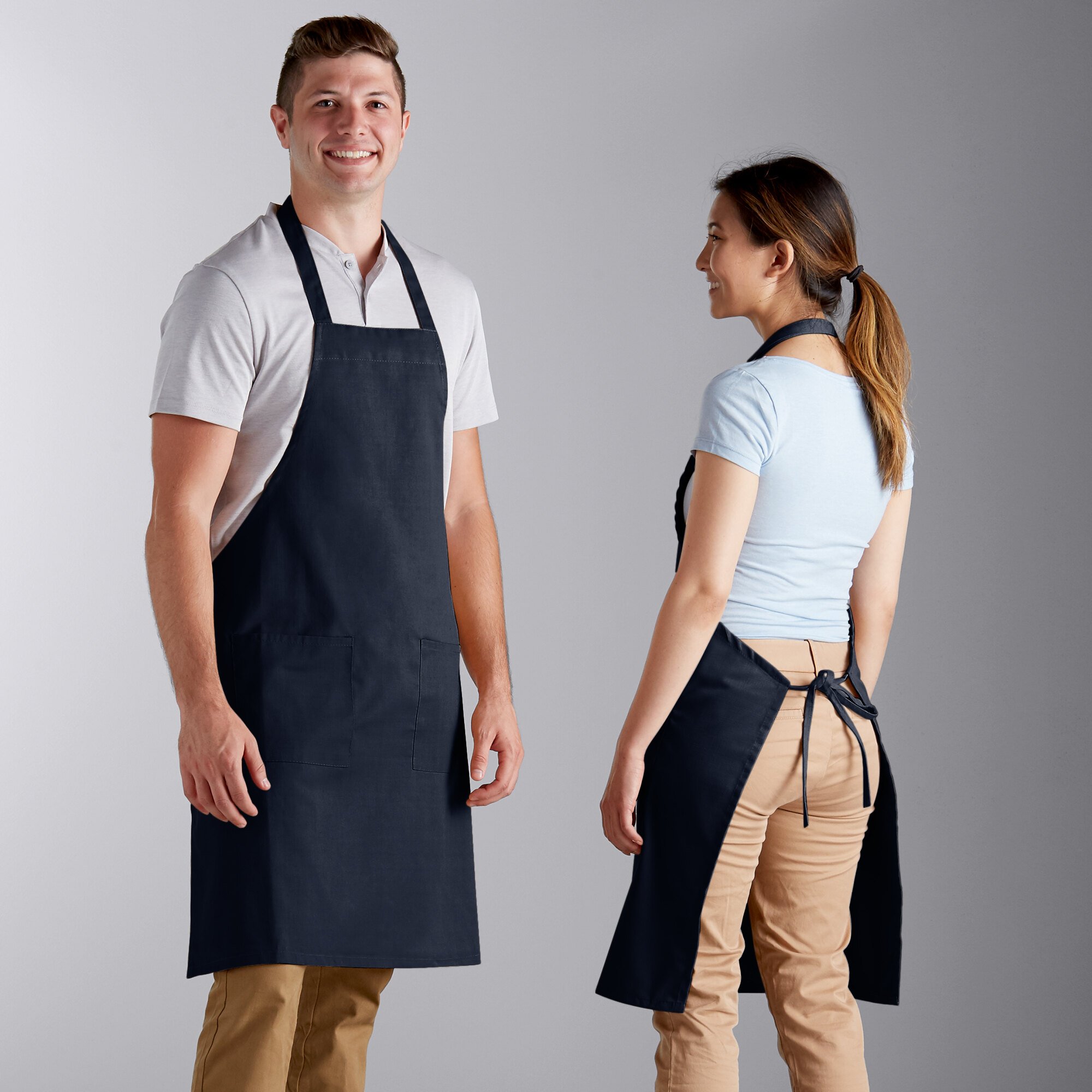
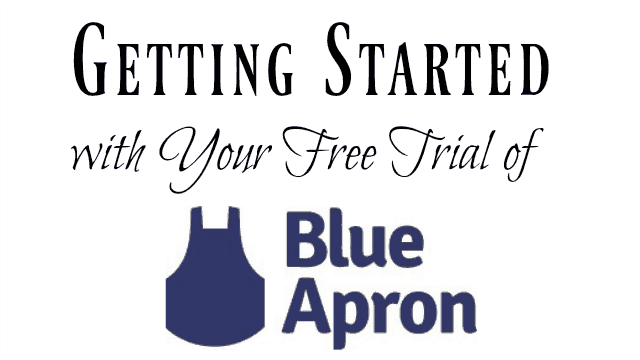
Containers, packages and pallets of all shapes and sizes needed to be stored. Our firm was able to work with Blue Apron’s plant management to devise a flexible storage and space plan to accommodate their needs. Producing meal kits that contain ingredients that differ from week to week creates the need for adaptable storage. We were able to improve upon the concept to create additional space for incoming materials, reduce travel distance for the product flow, improve the hygienic environment to produce the meal portions, and reduce the space needed for employee amenities.
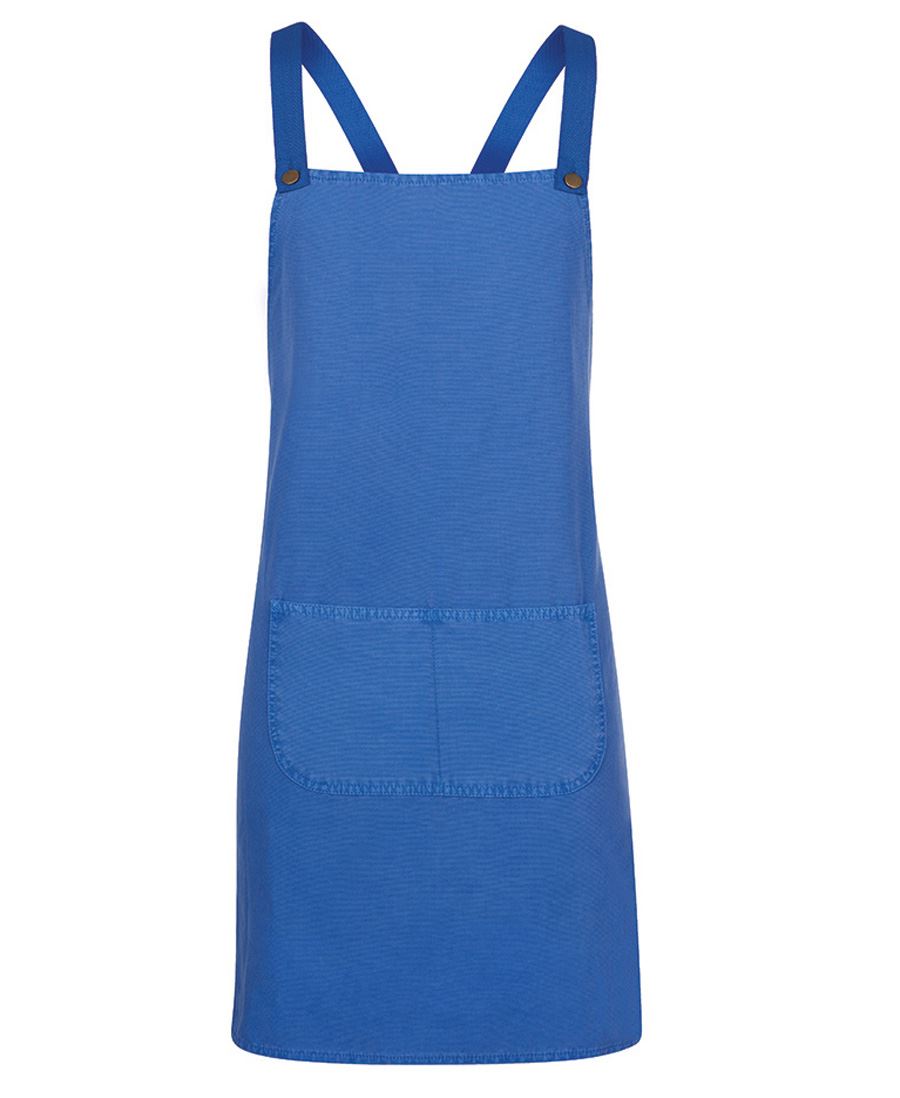
FPE project managers were given a rough concept layout from Blue Apron’s startup team. This project required not only a creative design mindset, but a thorough understanding of a unique operation that combines manufacturing with traditional ecommerce within the same building and business. The plant was originally conceived to produce meal kits with primarily manual means, but market demand grew to a point that only additional space and automation could address. Food Plant Engineering built-out the first 50,000 square feet of the original operation and was asked to look at expanding it once again. An exploding market for meal kits demanded an upgrade to Blue Apron’s southwest operation.
